BuildBlock ICF Design Advantages
BuildBlock ICFs are designed to provide advantages for contractors, builders, and home owners. Save time, money, reduce waste, achieve superior performance in your ICF project.
BuildBlock ICFs Are Fully Reversible Forms
BuildBlock ICFs are 100% reversible while the vast majority of all ICFs are non-reversible or only partly reversible. This means when you pick up a BuildBlock ICF, you don’t waste your time determining if the ICF needs to be turned up or down or left or right to be installed. With a reversible ICF like BuildBlock, it always fits no matter which way you turn it.
When it comes to corners, one BuildBlock ICF corner is the same for right or left applications. Non-reversible ICFs come in left and right-hand corners which create several disadvantages. First, our distributors tell us they can’t count the times when they’ ve picked up the wrong corner with other ICFs and marched to the far end of an installation only to find they needed the other hand corner. Second, when you get to the last course there is a good chance you will have the wrong corners (left or right) remaining.
The waste factor for fully reversible ICFs can be as little as 1 or 2%, while waste factors of 5% or more are common with non-reversible ICFs. When using products other than BuildBlock ICFs, you must take this into account, as well as the extra cost for the extra ICFs needed to do the job.
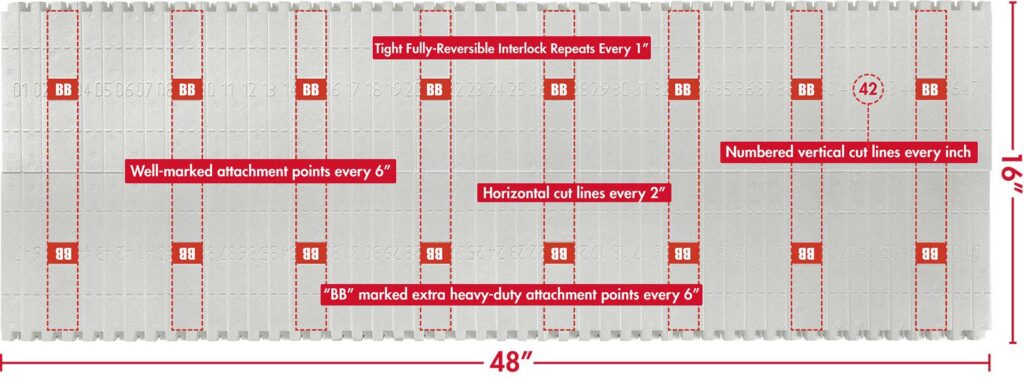
Building with ICFs decreases your utility bills 40%-60% each month and makes your home quiet, comfortable and disaster resistant.
BuildBlock Insulating Concrete Forms (ICFs) are the strongest and most energy-efficient building material available today. ICFs are used to build homes, schools, churches, and other commercial buildings. Choosing ICFs for your next construction project means saving money every month and feeling secure in your home.
See ICFs in action & learn more about building with icfs!
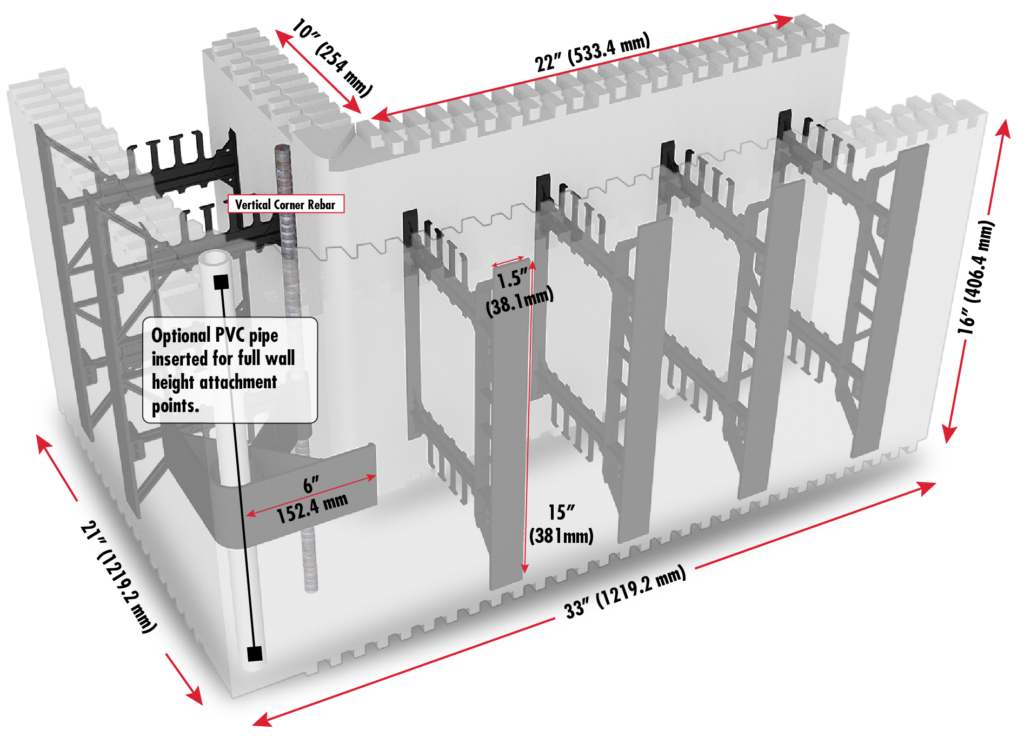
Longer Corner Blocks
BuildBlock 90° and 45° ICF corner blocks are 6″ longer on each leg than the industry standard. The many advantages this gives to our product include shorter offsets that get you past the crucial short offset. This eliminates many hours of extra corner bracing and extra strapping.
The longer corner blocks prevent corner pullout and head joints from opening up leaving you with a wall that isn’t plumb or straight. When corners pull out this can typically lead to blowouts which are common in the industry among other ICFs. The extended corner form significantly reduces corner shifting and enhances the overall stability of every pour. On a 4 to 5 day job, this can amount to a full days savings in labor costs.
Marked Horizontal & Vertical Cut Lines
BuildBlock ICFs have horizontal and vertical cut lines on both sides of the ICF which allow for much faster and more efficient installation times. The horizontal cut lines are an easy visual reference to ensure your forms are level and properly aligned. This saves countless time in the field and makes spotting inconsistencies quick and easy.
Numbered Vertical Cut Lines Every Inch
There is no longer a need to measure your vertical cuts. Simply note the measurement number on the block and cut on its line for a custom cut piece that fits every time.
Tight Horizontal Connections
BuildBlock ICFs have a tight interlock pattern repeated every inch. This interlock is so tight that it eliminates the need for special clips, zip ties, additional glue saving time, cost, and reducing complexity.
The BuildBlock 1-inch repeating pattern and its molded cut lines pre-align the installation of ICF forms and eliminate block alignment issues. This eliminates block misalignment and ensures the built-in furring strips line up, giving you a better job every time.
Built-in Half Height Blocks
BuildBlock ICFs are easily cut in half horizontally to make half height forms. The unique web design ensures that each half height form is identical. This allows for special height walls without wasting half a block or more on each cut. Use both halves and eliminate waste and extra cuts needed with other ICFs. This also eliminates the need to order special height forms (required by other systems). The built-in rebar fingers on the inside of the web hold rebar tightly in place reducing and eliminating rebar tying.
Running Bond Interlock & Block Bonding
BuildBlock ICFs bond out to even and odd inches from outside to outside and inside to outside corners. They also have a minimum bump factor of -inch when necessary. Of all ICFs in the industry that have interlocking nubs, most of them have a bump factor of 2 inches or more. (Some ICFs have up to a 6-inch bump factor.) Making adjustments in increments of 1″ ensures the least waste in the industry. This transforms into less waste on every project as well as walls that match the floor plans of your designs.
Self-Draining Interlock
The BuildBlock interlock connections are self-draining by design. When it rains, water doesn’t pool in the connections as can occur with other ICFs. Therefore, in freezing weather, there’s no water to freeze keeping you from stacking the next day until everything thaws. This sealing member in the interlock also prevents water from penetrating through the interlock.
Six-Inch Web Spacing & Attachment Points
BuildBlock ICFs have web spacing on 6-inch centers. Most ICFs come with 8 to 12-inch spacing on the webs. This cost-cutting feature reduces the overall performance and quality of the project and increases the potential for problems. The 6-inch spacing eliminates the scallop effect of the concrete pressure distorting ICF forms during the pour. A 6-inch web spacing creates the strongest ICF possible and further reduces the chance of any blowouts.
Two extra furring strips per block per side (which are part of each web) give sheet rockers more attachment points to fasten to. Webs are expensive and having two more webs in our ICFs gives you the most value added product on the market.
All furring strips are 15″ tall by 1.5″ wide per 16″ course and have two distinctive marked (sweet) spots on each furring strip at 8-inch centers vertically and 6-inch centers horizontally. These spots have a screw pull out strength that is roughly equivalent to wood or structural steel studs (close to 450lbs).
Deeper snap-in rebar saddles accommodate two #5 rebar and the patented corner tie is 6″ x 6″ wide and 2.5″ tall for simplified corner attachments. A
ll ties or furring strips are recessed 1/2-inch to allow stucco or EIFS applications as approved by the manufacturers.

