Environmentally-responsible construction
isn’t just a trend.
Green building is picking up momentum as more and more public and private building owners demand high-performance, earth-friendly construction methods, and materials.
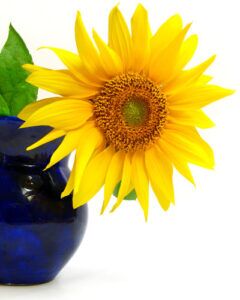
Sustainable construction and green building may take a little more effort and money up front, but this is truly outweighed by the lasting benefits and long-term savings for the building owner and the environment alike. And the fact is, as “green building” becomes the norm, its practicality and affordability will increase. It just takes forward-thinking, concerned home buyers, homebuilders, developers, contractors, and architects to pioneer and establish its practice.
The ongoing energy use of a building is probably the single greatest environmental impact of that building and continues to impact the environment for decades, even centuries. So the opportunity to choose a building material — like insulating concrete forms — which can significantly decrease its energy consumption, shouldn’t be taken lightly.
Can’t you spare a little change for Mother Nature? The future will thank you. The lower utilities costs and increased comfort will reward you.
What is LEED?
As you research the subject of green building, you’ve undoubtedly encountered the term: LEED®. The LEED (Leadership in Energy and Environmental Design) Green Building Rating System® is a voluntary, consensus-based national standard for developing high-performance, sustainable buildings. Members of the U.S. Green Building Council representing all segments of the building industry developed LEED and continue to contribute to its evolution. BuildBlock Building Systems LLC is a proud member of the USGBC.
LEED provides a complete framework for assessing building performance and meeting sustainability goals. Based on well-founded scientific standards, LEED emphasizes state of the art strategies for sustainable site development, water savings, energy efficiency, materials selection and indoor environmental quality. LEED recognizes achievements and promotes expertise in green building through a comprehensive system offering project certification, professional accreditation, training and practical resources. (Excerpt from U.S. Green Building Council’s website.)
LEED was created to:
- define “green building” by establishing a common standard of measurement
- promote integrated, whole-building design practices
- recognize environmental leadership in the building industry
- stimulate green competition
- raise consumer awareness of green
- building benefits
- transform the building market
What is LEED certification?
Companies and products are not LEED Certified. Actual structures can earn LEED Certified status by earning points for various green building elements. There are four levels of LEED Certification:
LEED® Certified | 40 – 49 Points |
LEED® Silver | 50 – 59 Points |
LEED® Gold | 60 – 79 Points |
LEED® Platinum | 80 – 110 Points |
How BuildBlock ICFs Can Contribute to 19-46 LEED Certification Points
The following is a third-party assessment conducted by Kelly Parket, P.E. a LEED Accredited Professional who is President of GWS, LLC.
How BuildBlock ICFs Can Contribute to 19-46 LEED Certification Points
The following is a third-party assessment conducted by Kelly Parker, P.E., a LEED Accredited Professional who is President of GWS, LLC.
BuildBlock Building Systems Insulating Concrete Forms (ICFs) can help your construction project attain Leadership in Energy and Environmental Design (LEED) Green Building status. BuildBlock ICFs are a clear choice for building designers to maximize points in the LEED rating system.
19 – 27 Points: BuildBlock ICFs can furnish the basis for 19 LEED points if the guidelines outlined below are applied in the building design and construction. Another 8 LEED points can be achieved indirectly because of the highly synergistic thermal control qualities of BuildBlock ICFs. These possible added points are highlighted in blue in the following synopsis. | ||||
BuildBlock ICFs consist of foam insulation forms for poured concrete walls that stay in place as a permanent part of the wall assembly. The forms are interlocking blocks connected with high-density plastic webs. The stay-in-place forms provide a highly effective insulation, a sound barrier and a backing for exterior and interior wall materials (drywall, siding, brick, etc.). The ICFs can contribute to attaining LEED credits including: Sustainable Sites (SS): | ||||
| ||||
LEED Intent: Conserve existing natural areas and restore damaged areas to provide habitat and promote biodiversity, such as limiting all site disturbance to 40 feet beyond the building perimeter. | SS Credit 5.1 calls for reducing the development footprint and limiting site disturbance in order to conserve existing natural areas. BuildBlock ICF construction can help reduce impact to a construction site, as the bracing is typically erected on the inside of the ICF wall, with limited construction activity around the perimeter. | |||
| ||||
LEED Intent: Reduce heat islands (thermal gradient differences between developed and undeveloped areas) to minimize the impact on microclimate and human and wildlife habitat. | BuildBlock ICF affords the building owner many choices in exterior finishes. Light colored, highly reflective finishes and surfaces can readily be chosen to help achieve this LEED point. (While ICF itself does not contribute directly to achieving the heat island reduction, it does afford the flexibility required in choosing exterior finishes.) | |||
Energy & Atmosphere (EA): | ||||
| ||||
LEED Intent: Establish the minimum level of energy efficiency for the proposed building and systems. | Prerequisite 2 states that the building must meet the mandatory and the performance requirements defined | |||
| ||||
LEED Intent: Achieve increasing levels of energy performance above the baseline in the ASHRAE Standard 90.1 to reduce environmental and economic impacts associated with excessive energy use. | The LEED – NC rating system identifies energy savings as the most heavily weighted criteria, with up to 10 points achievable for buildings designed for energy savings over and above the base requirements defined in the ASHRAE Standard 90.1–2004. The high-performance thermal envelope of BuildBlock’s ICF construction can realize more than the 17.5% energy savings vs. the base to achieve the 3 points. | |||
| ||||
LEED Intent: Encourage and recognize increasing levels of on-site renewable energy self-supply in order to reduce environmental and economic impacts associated with fossil fuel energy use. | BuildBlock ICF will help to ensure a significant reduction in the total energy use of the building. Therefore, the increased percentage of energy produced by an on-site renewable system (12.5% or more of the total energy) will be much easier to achieve. | |||
| ||||
LEED Intent: Encourage the development and use of grid-source, renewable technologies on a net zero pollution basis. | BuildBlock ICF will help to ensure a significant reduction in the total energy use of the building. Therefore, the increased percentage of energy produced by a grid-source, renewable system (35% or more of the total energy) will be much easier to achieve. | |||
Materials & Resources (MR): | ||||
| ||||
LEED Intent: Extend the life cycle of existing building stock, conserve resources, retain cultural resources, reduce waste and reduce environmental impacts of new buildings as they relate to materials manufacturing and transport. | Walls in existing buildings constructed with BuildBlock ICFs can be easily reused. The ICF’s superior energy saving performance will make their reuse almost a certainty. This extends the life of buildings, conserves resources, and reduces waste, minimizing the environmental impacts of new buildings due to manufacturing and transport. (While ICF itself does not contribute directly to achieving the building reuse on the current project, its durability does contribute to extending the life cycle of the building being constructed, | |||
| ||||
LEED Intent: Divert construction and demolition debris from disposal in landfills and incinerators. Redirect recyclable recovered resources back to the manufacturing process. | BuildBlock ICF’s waste is 2 – 5% compared to the normal waste of alternative construction methods. This provides a significant contribution to the overall potential for construction site waste reduction. By comparing the typical ICF waste factor of 2 – 5% with the normal waste factor of the alternative construction method, the LEED AP can identify the quantities diverted. | |||
| ||||
LEED Intent: Increase demand for building products that incorporate recycled content materials, thereby reducing impacts | BuildBlock has incorporated recycled content in the ICF plastic web ties. The polypropylene used for the webs in the forms contains post-industrial (factory regrind) waste. The concrete mix used for ICFs can incorporate high percentages of fly ash, which is 100% post-consumer recycled. The reinforcing steel is generally 80% or more post-consumer recycled. For LEED calculations, the recycled content is determined by weight. The recycled fraction of the assembly is then multiplied by the cost of assembly to determine the recycled content value. The values of all the materials used in the building are added for a combined percentage. The required 20% recycled content is very achievable. | |||
| ||||
LEED Intent: Increase demand for building materials and products that are extracted and manufactured within the region (within 500 miles of the project site), thereby supporting the use of indigenous resources and reducing the environmental impacts resulting from transportation. | Depending on the building project location, some of the BuildBlock ICF materials may have been manufactured within the 500-mile radius. The aggregate for concrete certainly would qualify. The percent of regional materials is determined based on the ratio of their cost to the total materials cost for the project. | |||
| ||||
LEED Intent: Encourage environmentally responsible forest management. | The need for wood framing materials is reduced when BuildBlock ICF materials are used. This reduces the need for wood on the overall project. Thus, the higher unit price for certified wood is minimized in the cost impact on the overall project and makes certified wood an easier choice. (The positive effect of using ICF is an indirect impact on this credit. But the significantly lower total quantity of wood will make Certified Wood easier to justify the overall cost of the project and thus lead to gaining this LEED point.) | |||
Indoor Environmental Quality (EQ): | ||||
| ||||
LEED Intent: Establish minimum indoor air quality (IAQ) performance to enhance indoor air quality in buildings, thus contributing to the comfort and well-being of the occupants. | Post-construction, BuildBlock ICF releases no VOCs or air-borne particulates. The ICF walls have very low air infiltration. The minimum requirements for ventilation defined in Sections 4 through 7 of ASHRAE 62.1-2004 can easily be met without the concern for contaminants contributed by the ICF envelope materials. | |||
| ||||
LEED Intent: Provide additional outdoor air ventilation to improve indoor air quality for improved occupant comfort, well-being, and productivity. | The BuildBlock ICF insulation, combined with the reduced air infiltration of the ICF assembly, result in an interior airspace that is “neutral.” There are no convective currents caused by temperature fluctuation of the wall material. Nor are there any drafts caused by air leaks. The ambient temperatures throughout the space show little variance. With such a controllable airspace, the HVAC designer has a much easier task of achieving the intent of increased ventilation while minimizing additional energy consumption. | |||
| ||||
LEED Intent: Reduce indoor air quality problems resulting from the construction/renovation process in order to help sustain the comfort and well-being of construction workers and building occupants. | The EPS foam used in BuildBlock ICF forms emits no VOCs, formaldehyde or other contaminants. The ICF | |||
| ||||
LEED Intent: Reduce the number of indoor air contaminants that are odorous, irritating and/or harmful to the comfort and well-being of installers and occupants. | The BuildBlock ICF product emits no VOCs, formaldehyde or other contaminants. Low VOC adhesives and/or caulks required in the associated construction seals can easily be chosen to keep below the overall VOC emission limits required. | |||
| ||||
LEED Intent: Provide a high level of thermal comfort system control by individual occupants or by specific groups in multi-occupant spaces to promote the productivity, comfort, and well-being of building occupants. | The BuildBlock ICF contributes significantly to the improved energy performance of the building. This improves the controllability of the load on the HVAC systems. Therefore, the building can be designed for better occupant control of temperature, humidity, and ventilation including the use of operable windows. (While ICF itself does not contribute directly to achieving the better controllability, it does afford reduced exterior load disturbances on the HVAC system leading to better controllability.) | |||
| ||||
LEED Intent: Provide a comfortable thermal environment that supports the productivity and well-being of building occupants. Assess the thermal comfort of the building. | The BuildBlock ICF contributes significantly to the improved energy performance of the building. This makes it easier to design and operate the building HVAC controls for temperature, thermal radiation, humidity and air flow. The improved energy performance of the building envelope also makes it easier to design and implement a building thermal comfort monitoring system. (While ICF itself does not contribute directly to achieving the better thermal comfort, it does afford reduced exterior load disturbances on the HVAC system leading to better thermal comfort.) | |||
| ||||
LEED Intent: Provide for the building occupants a connection between indoor spaces and the outdoors through the introduction of daylight and views into the regularly occupied areas of the building. | The BuildBlock ICF contributes significantly to the improved energy performance of the building. This increases the controllability of the load on the HVAC systems. As a result, the building designer has more options for ventilation and the location, size, and orientation of windows. A window layout that improves daylighting is much easier to achieve. (While ICF itself does not contribute directly to achieving the better daylight and views, it does afford reduced exterior load disturbances on the HVAC system. This, in turn, gives the designer more flexibility for window location, size, and orientation as well as the use of windows for ventilation.) | |||
In addition to the benefits defined in the USGBC LEED system, ICFs contribute to sustainable construction in many other ways. The sound dampening of the concrete and foam is ideal for protection from urban noise. The solid monolithic concrete wall withstands the worst of rainstorms, fires, and high winds. It is also a barrier to insects, including termites. | ||||
GWS is a National Engineering, Consulting and Inspection Firm with corporate offices in Oklahoma City, Oklahoma. (www.gwssi.com) GWS is building a national network of Raters and LEED Professionals to build and certify energy and resource efficient structures. We utilize the latest computer modeling to give full benefit to all rated components. Our national network of Raters can facilitate your project’s certification. GWS would be happy to work with you to market this process to your clients. | ||||
Prepared by: Kelly Parker, Professional Engineer LEED AP | ||||
How to Achieve LEED CertificationIt very important to involve a LEED Accredited Professional in your project from the beginning. You can locate a LEED AP in your area by visiting the LEED AP Directory on the US Green Building Council’s website. |