How to Build: Door & Window Openings
This page will discuss design considerations of ICF doors & windows in an ICF wall as well as material options and construction of bucking for ICF Door & Window Openings.
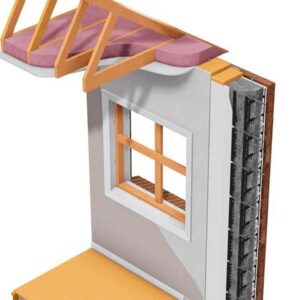
Designing Openings and Spacing for ICF Windows & Doors
Anything is possible with ICFs, but using the guidelines below can prevent additional engineering requirements or challenges during construction.
1.) Space openings no less than 12”. If the spacing is less than 12”, mull or frame the openings as a single opening. If openings must be spaced closer, take extra care to ensure complete consolidation between openings and add additional rebar as needed.
- Provide minimum space for adequate consolidation of concrete beside openings. IRC & IBC require internal vibration for all walls.
- Mulling smaller openings together may reduce overall vertical rebar beside openings (through eliminating multiple openings). Place rebar as scheduled beside openings (typically 2 bars on each side of the opening).
- Ensure that proper lintel design is followed for wider openings including stirrups if required.
2.) Openings should be spaced not less than 12” from a corner. If openings are spaced closer, extra care should be taken to ensure complete consolidation in the corner form with additional bracing and strapping. The corner form and buck may try to separate from each other unless braced and strapped properly.
- Jambs for garage doors and other large openings should be a minimum of 12”. If narrower, lintel steel should still extend into adjacent walls the required 24” beyond opening on each side.
- Use pre-bent steel for wrapping corner lintels. If discontinuous steel is used, then a 40X bar diameter overlap is required
- Take extra care to ensure complete consolidation in the jambs. IRC & IBC require internal vibration for all walls.
3.) Doors with side-lights should be framed together unless adequate spacing for concrete is available as noted above.
- In applications where full height sidelights are not used, windows should be framed with the door, with ICF wall extending below the window.
- Vertical steel should be placed on each side of the opening as scheduled.
- Lintel reinforcement should extend 24” beyond the maximum width of the opening.
- Additional vertical steel may be placed beside the door, and extend to below the window.
Window & Door Bucking Options
Openings in ICF walls must stop the flow of concrete and provide attachment points for the installation of doors or windows. This process is called bucking. It is the same concept as completing end walls or bulkhead walls. The bucking size and type are usually determined by the type of opening and the needs of the product to be installed. Consult door or window manufacturers for any specific needs during plan review.
Bucking is generally a permanent part of the wall once the concrete is poured. This creates attachment points for windows and doors and wall finishes. This section addresses the most popular types of bucking material: Treated Wood, Metal, Vinyl Bucking, and ICF Foam Bucking.
BuildBlock recommends that bucks be pre-built. This will ensure correct sizing, saving time and labor. It is critical that the type of buck material and its thickness be correctly accounted for when creating rough openings. Also, bucking should be braced appropriately to ensure it says in place during the pour and remains square and plumb. Bracing horizontally and vertically is required to prevent the buck from shifting due to the concrete forces which could prevent the installation of the door or window without major structural changes.

See ICFs in action & learn more about building with icfs!
ICF Foam Bucking (Most Preferred Method)
In the last few years, ICF Foam bucking has become more popular. ICF bucking uses the same materials as the ICF walls, giving you the same advantages. This provides the same type of insulation and attachment that ICF blocks use.
ICF foam bucking uses a plastic embedded web made from either polystyrene or polypropylene and EPS foam. First, choose a foam buck that is designed for the size block being used. After that, the ICF bucking must be completely braced on the inside of the opening. This is accomplished by building a frame inside the opening as well as using diagonal braces on corners to ensure the opening remains square.
Installation Notes
- Keep in mind the thickness of the bucking material and ensure the rough opening is sized correctly for the required opening size.
- We recommend 1/2” extra for width & height. This allows 1/4” completely around the window or door. Poured concrete is hard to adjust.
- Brace each opening by building a complete frame inside the opening with cross braces. Add diagonal braces to ensure opening remains square during the pour.
- Recheck all openings for square and plumb before and during the pour. There is only one chance to get it right.
Other Methods
There are two ways to use treated dimensional lumber to buck a BuildBlock wall opening. Treated wood can be placed inside the wall cavity or across the width of the form. Each has both advantages and challenges.
- Treated wood can be mounted inside the ICF wall cavity and is sometimes referred to as a sub-buck.
- Rip the 2X material to fit into the void of the wall.
- Use foam adhesive and screws with plastic cap washers inserted from the side to secure the buck every 6” on both sides around the opening.
- Match or rip width of the lumber to the block width.
- This utilizes the entire width of the dimensional lumber and covers the entire profile width of the block.
- With both methods, it is recommended that you use 6” galvanized ring shank nails, anchor bolts, or tapcons set through the wood into the void area so the concrete can capture the nails and the bucks remain adhered to the concrete when the bracing is removed. Alternate these to the left and right of center every 8” to 12” up and down the buck and across the header and window sills.
Metal bucking systems incorporate a support flange that fits around an ICF wall. These systems are cast in place to provide an extremely solid support for windows or doors. Typically, metal bucks or door frames are used in specialty applications such as explosion resistance. It is also possible to install steel door frames and pour them in place. This is very similar to bucking where the frame itself becomes a buck.
If required, some metal bucking systems exist that can be removed after pouring concrete to provide exposed concrete. Also, metal bucking systems can be used to create a fire break between the outside and inside walls. However, this is an uncommon practice.
Additionally, wood frame bucking could accomplish the same task if removed after pouring. If using this method, do no use the 6” ring shank nails.
Bucking Construction
Door Buck Construction
Start by knowing the required rough-in dimensions for all openings. You can obtain this information from your window and door suppliers. Make sure the inside dimension is large enough to allow for your door system jambs and shimming to plumb your installation. Door bucks will usually only have three parts – two sides and a top. Use temporary support at the bottom when bucks are placed to keep it aligned. Bucking should be removed after the concrete is poured.
Angle brace all bucks to keep them square and true.
Window Buck Construction
Window bucks differ from doors in that they have a bottom. If using wood, you can use treated 2x4s on the bottom, spread out to the outside, allowing a space in the middle to fill under the openings with concrete. Also, it’s important that the bottom pieces fit inside the sides to act as a brace for concrete pressure pushing inward.
If using Vbuck or foam bucks, a 4” hole saw on 12” centers will make ample holes for you to fill the underside of the opening in order to eliminate voids in this area. After the pour, clean the bucks with a towel while the concrete is fresh. It’s much easier to do this now than later, and you’ll have a nice clean opening when you are finished. A clean job also encourages other trades to do higher-quality work.
Lastly, keep inside dimensions or rough openings large enough to allow for proper window placement and shimming if necessary. It’s very difficult to make an opening larger if the window doesn’t fit. So, keep in mind that a little extra space goes a long way.
Let Us Help
Contact BuildBlock today and let our staff answer your questions and help make your project a success.