Tips and Best Practices When Designing Your ICF Home
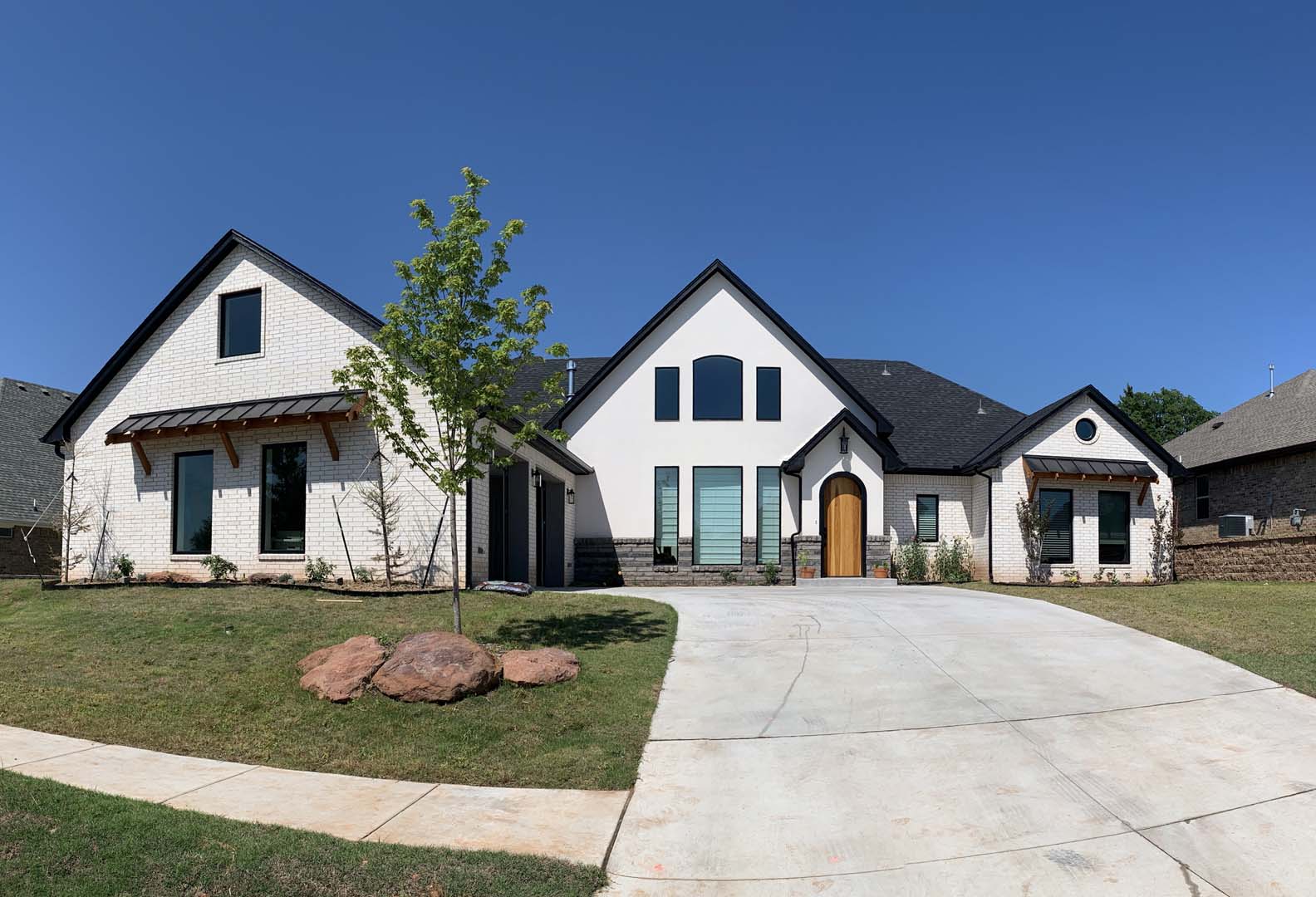
by Justin Wallace, Technical Director
At BuildBlock we’re often asked for advice to help those who are designing an ICF structure. We try to answer technical and design questions that might arise during the design process to help make building your project as easy as possible. In this article, I’ve compiled some tips and best practices for answering a few of the most common questions to help design your ICF home. If I’ve missed something you think we should talk about, reach out and let us know.
In this article I’m going to touch on five areas to help you design your ICF home:
- General Design Dimensions and Standards
- Windows (and door openings)
- Plumbing & Electrical
- HVAC Design (And adequate ventilation)
- Building Codes & Local Regulations
- Geotechnical Reports
- Ways to maximize performance and savings
Design Basics
When designing an ICF house, designers often try to design using dimensions that fit the blocks rather than defaulting to standard construction dimensions. While keeping block measurements in mind may seem like it makes easier it could actually make construction harder. There are a few considerations to keep in mind: windows too close to corners; window and door heights based on block coursing, and avoiding short returns on corners, but generally you should design that structure the way you want it.
The most cost-effective way that I’ve found is to keep the exterior dimensions based on a standard pattern (8″, 12″ 16″, or 48″ increments.) This matches the same layout as most construction materials which are based on an 8″x8″ repeating pattern. Any ICF block can have up to 1/16″ of variance due changes in temperature and humidity which affect overall dimensions.
Another tip when designing your ICF home is to stay away from tight jogs in the wall. When you’re building a 13″ wide wall (8” ICF plus 5” of EPS foam), it becomes very difficult to integrate a 12″ jog in the wall. Keep any jogs to at least 2-feet if you can. That way you can avoid dealing with any challenges from tight jogs altogether.
When it comes to the upstairs, make sure that any upper level ICF wall is also supported by an ICF wall below. Concrete walls are very heavy, and engineering can become difficult if there is not another concrete wall below to carry the load above. In general, it’s best to limit ICF use to exterior walls, unless you need a load bearing wall, a fire wall, demising wall, or sound attenuation in an interior room such as a home theater room or drums practice room studio.
Doors & Windows
Planning door and window openings in your design is also a key step. It’s important to place windows on the exterior of the opening and attach doors to the interior. This ensures doors can open wider than 90-degrees.
When selecting building materials, consider choosing products a step above “builder grade”. For example, I’m in Colorado and was introduced to Alpen Windows many years ago. They use a thin, super clear plastic film in their windows, making them perform similar to a triple pane window, while costing significantly less. There are many options for windows and doors, so do your research in advance.
Just as you wouldn’t install the cheapest tires on a Ferrari, building highly energy-efficient walls and then compromising those walls with a poor choice for windows and doors will prevent you from fully realizing the potential energy savings and comfort in your home. Make choices that match your needs and budget.
Sometimes small choices can make a big impact during construction. My perspective from designing and planning openings includes considering the heights of doors and windows and where they are placed in the ICF wall. Standard doors are 80” tall. ICFs are 16” tall which course out with a horizontal joint right at 80”. This seems like it would benefit your design, but doors have an additional 2” of bucking material at the top and on each side which makes your opening height 82” tall. This height requires cutting into the course of blocks above the door and puts you in the middle of the rebar fingers of each web. If this only mattered for a few doors, it wouldn’t be a major issue, but you typically match the height of windows with doors. This means every opening now has the same interference problem, requiring cutting or clipping hundreds of rebar fingers.
A simple change, if your design allows for 7-foot doors rather than 6’-8”, realigns openings above those web/tie rebar fingers. This saves time and labor on the construction side of the equation. Unfortunately, 8-foot doors set you up for the same problem; it’s not the end of the world but this is an area where unforeseen work is required during the build.
Plumbing & Electrical
I think one of the biggest questions I get is about where plumbing goes when building an ICF home.
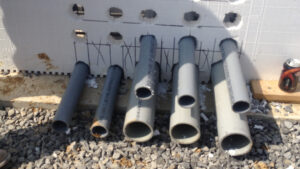
You’ll need to keep 2 things in mind: there will be penetrations that allow pipes, wiring, telecommunication and other systems to pass through the wall from the outside to the inside, and you’ll need a place to hide mechanical, electrical, and plumbing (MEP) items behind your walls. Penetrations are done by placing sleeves in the wall before the pour. The sleeves are then cut flush with the wall after the pour to prepare for wall finishes and mechanical installation.
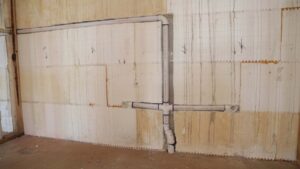
When planning chases for plumbing and electrical, it’s important to understand that larger (3”-4”) plumbing lines can potentially lead to fitment issues, and it’s recommended that you use smaller lines where possible. The EPS panels on both sides of the block have a thickness of 2.5” and if you use smaller lines, the chases can be made directly in the EPS panel. Additionally, toilets should be placed on interior walls, if possible, to accommodate the size of pipe used for waste drains and venting. This gives you full design latitude for all other supply and waste lines for plumbing and electrical runs.
The actual plumbing pipes are not ever placed in the concrete cavity as that would weaken the structural wall and make maintenance or repairs challenging. Instead, after the walls are poured, the pipes or wiring are placed in the foam where needed. The EPS foam can be easily removed to create a chase in the foam to run lines horizontally and vertically. Pipes that are larger than 2” should be run on interior walls if possible.
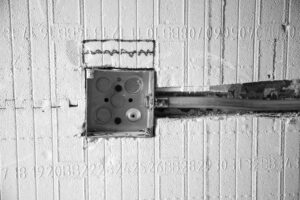
Electrical wiring is done the same way. The wire is pushed back against the concrete core after the wall is poured and held in place by spot– gluing it every few feet. Standard electrical boxes may be used and attached to the concrete core directly or ICF electrical boxes may be used that attach to a web tie / flange. Learn more on our website and YouTube channel at https://buildblock.com/how-to-build-an-icf-home/rough-ins-plumbing
Heating, Ventilation, & Air Conditioning (HVAC)
ICF walls offer incredible insulation properties and BuildBlock ICF blocks alone offer an insulation value of R-23., Even better, this airtight wall when fully assembled and finished will perform at closer to an insulation value of R-50. This high-performance insulation and airtightness reduce the overall HVAC requirements of the structure. An HVAC installer who understands the air-tight building envelope that ICFs provide is able to tailor HVAC equipment sizes to correspond to the structure’s insulation performance. This is particularly beneficial for realizing your design and performance vision without wasting heating or cooling capacity that will never be efficiently utilized.
It’s also important to note that when “Manual J” calculations for your design are submitted to your building department, you need to be as accurate as possible to maximize your HVAC savings. You might also consider integrating ERVs, HRVs, or even ductless mini split systems into your ventilation design, where appropriate, to help maximize savings.
A ductless mini-split HVAC system, or mini-split, is a type of air-conditioning and heating system that uses individual, wall or ceiling mounted blowers to provide temperature control in one room or area. Instead of using ductwork, the individual units are connected by a refrigerant line set to a single outdoor condensing unit. You may have seen these systems in small apartments or other spaces while on vacation, in coastal areas or tropical areas where they are very efficient and popular.
Following these steps will help ensure that your structure is built in the most cost-effective way possible and deliver maximum HVAC savings over the lifetime of the structure.
Building Codes & Regulations
All building codes are local. Many states and municipalities base their codes on national or international standards but may have some local differences. Because local building codes vary, depending on the municipality and region, find out from your local code office if they accept prescriptive engineering from manufacturers. If they do, download the BuildBlock Flat Wall Engineering Manual from https://buildblock.com/technical-support/engineering-tables/ and use them as a guideline.
This will spare you the expense of having to hire a structural engineer to design the entire project. If they don’t accept prescriptive engineering, we have a long list of engineers we’ve used in every state we can connect you with. They will be able to use our engineering as a starting place for your specific project.
If you use light frame roof trusses, they will likely have an on-staff engineer to work through that component; however, the floors, interior walls and most other components that will likely be inspected are already written into the code, you’ll just need to follow the existing guidelines.
Geotechnical Reports
Another important step that can potentially save you thousands is a quality Geotechnical report. A detailed and accurate Geotech report is worth its weight in gold. Geotechnical reports are documents that provides information about the ground conditions of a proposed building site, as well as design recommendations and advice. Geotechnical engineers use reports to communicate site-specific design parameters and construction recommendations for the geotechnical components of a project. These recommendations can include foundations, excavation, groundwater conditions, retaining walls, ground anchors, and earth works.
For example, during design, it’s hard to size footings if you don’t know how much bearing capacity your soil has, and the requirements for waterproofing can largely be determined by the hydrostatic properties that you will discover in that report. Most reports cost around $1,500 and it’s worth the investment to know your site’s needs before you start. You could save money by learning the requirements are much less than you budgeted for, or by informing you in advance that the requirements are higher than anticipated and stating the additional steps up front to prevent costly fixes on the back end.
Maximize Your Savings & Performance
To get the most savings out of an ICF structure, build with ICF all the way to the roof. Building an ICF foundation or basement is a great place to start, and you’ll be able to enjoy a very strong and comfortable DIY basement. Continuing that savings and resilience by using ICFs for exterior walls all the way to the roof. This is where you’ll see the highest return on investment. The benefits add up quickly and can save you money in a big way. The other benefits such as disaster resilience and comfort will continue long into the future too.
Complete ICF building envelope homes typically operate on just 50% of the energy that comparable, traditionally built structures use. The cost difference of building with ICFs can be repaid within the first three to five years of operation through the energy savings.
Insurance Savings
Another way that ICFs save money is on the cost of insuring the structure. Not only do ICFs deliver strong, disaster resilient structures that are built to last, but ICFs are considered masonry (non-combustible) construction and as such, ICF homes typically see a 20% reduction in the cost of insurance premiums. You’ll need to work through the specifics with your insurance agent, but the benefits and savings are proven. Additionally, ICFs alone complete nearly every requirement for the Fortified Building Program. This program can deliver significant additional savings based on your location. Visit fortifiedhome.org for more information.
Closing It Up
ICFs are the perfect solution for building any type of structure and integrate amazingly well with virtually any design and most other construction materials. ICFs offer far more benefits and savings than traditional materials and are designed to last. I wanted to take a few minutes to share some of the basic questions I get asked and we hope this helps you make the best choice for your next construction project.
These are just some of the ways to maximize the cost-effectiveness of your ICF build. By giving a little extra attention to the design, you’ll be able to reap more benefits out of your project, both during construction and over the lifetime of the structure.
BuildBlock Resources
If you need more information about BuildBlock ICFs, whether technical details or installation information, we’re here to help. For architects and designers, our comprehensive CAD Detail library with over 300 standard connections and design details is available for download buildblock.com/technical-support/cad-details. We have an extensive online training program at buildblock.com/training and a robust YouTube channel youtube.com/buildblockicf with training, how-to, project profiles, and more.
Our technical team speaks with more than 75 years of combined experience in designing and building with ICFs. We’re dedicated to helping you achieve a successful build. Please reach out to us if you have any questions or need help during the design or construction process and we’ll be happy to help.
Oh, and if you’re building your project with BuildBlock, we’d love to see how it’s going every step of the way. Share you project with us at buildblock.com/myproject.