Cold Weather Concrete Construction
Building with ICFs in Cold Weather by Justin Wallace
Concrete plays a critical role in modern construction, forming the foundation of many structures and in some cases, building the entire structure, such as in ICF construction. Despite its cost-effectiveness, concrete has specific requirements during installation. Primarily, it requires a significant amount of water for proper formation and placement, but freezing temperatures during the curing process can pose a major challenge, particularly in colder climates.
Insulating Concrete Forms (ICFs) are uniquely suited for cold-weather construction. As an ICF contractor in Colorado, I’ve faced these challenges on more than half of the projects I’ve worked on, and I’d like to share some insights that have helped me navigate these conditions.
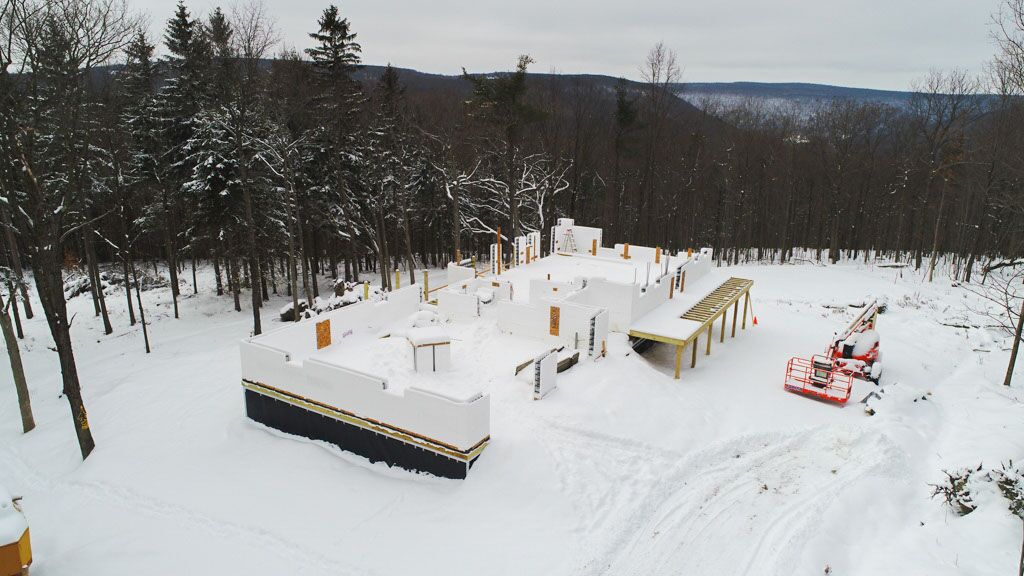
When bidding on projects likely to be impacted by snow or freezing temperatures, it’s important to recognize that no crew, no matter how skilled, can fully control the weather. A jobsite covered in ice or mud will inevitably slow down progress. Every morning, time is needed to clear snow from walkboards, pathways, materials, and equipment. At the end of the day, more time is spent covering materials, wall cavities, and tools to prepare for the coming cold. Expect to increase labor hours by 25%-30% to account for these additional tasks. Moreover, walking around the site with heavy, mud-caked boots can significantly slow your pace.
While most tools function in sub-freezing temperatures, not all perform reliably. For example, oil-less compressors use plastic piston rings that can crack in the cold if not properly warmed up. Similarly, many modern battery-operated tools have built-in low-temperature shut-off circuitry. To minimize damage and increase productivity, consider warming tools before use—such as by transporting them in the truck’s cab rather than the bed.
ICF construction provides a natural advantage in cold-weather conditions, but a few important considerations must be made. Nearly all ICFs today use high-density polypropylene web ties. The manufacturers “recipe” can be slightly adjusted for better cold-weather performance, but plastic remains brittle at low temperatures. Fortunately, most web ties are black, allowing them to absorb some heat from the sun during the day. Still, these ties should be handled with care. Rebar should be gently pushed into place, and screws should be used to attach bracing or boards instead of nails, which can cause the brittle plastic webs to crack.
EPS foam, although less affected by cold temperatures than the web ties, can still become more brittle. It’s crucial to protect foam connections from snow and ice buildup. One of the most frustrating lessons I learned early on in winter projects was spending hours chipping ice out of form connections with a screwdriver. The solution is simple: cover the forms. This applies to both the connection fingers and the empty concrete cavity.
As Technical Director at BuildBlock, I’ve seen firsthand the consequences of neglecting this step. One project had snow compacted beneath a concrete pour, which created a void in the wall around the entire project once the snow melted. An engineer recommended scraping the structure and starting over. Removing snow before the pour is time-consuming and labor-intensive, even with forced-air heaters. It’s far more efficient to cover the forms with a tarp, board, plastic sheeting, or the cardboard trays from the ICF bundles at the end of the day to prevent snow buildup and protect the connections.
Regarding the pour itself, ensure that your concrete provider includes hot water in the mix to maintain proper temperature. Organize your job site and pre-mark bolt and embed placements, as delays can cause the concrete pump to freeze or slow. In my experience, the pour process in cold weather is similar to warmer conditions, but extra care should be taken in areas prone to movement, as the cold affects the strength and brittleness of the materials. Additionally, walkboards and ladders can become slippery with even a small layer of frost, so exercise caution when working at height.
After the pour, smooth the top surface, place bolts and plumb the wall as quickly as possible, then cover the concrete with an insulated blanket. A tip: Many contractors sell their insulated concrete blankets on Craigslist after their project, often at half the price of new ones. I’ve found good deals on used blankets, which work well with ICFs since the forms insulate the sides of the walls unlike their traditionally formed counterparts. A 4’ wide sidewalk blanket is often enough to cover the top of the wall. The goal is to maintain a temperature of 50°F for 24-48 hours after the pour. Don’t forget to protect openings where concrete is exposed.
In conclusion, ICFs are an ideal solution for concrete construction in cold weather. With proper planning, the right equipment, and a few precautions, construction can continue well into the winter months, extending your work season and increasing your company’s profit potential.
For more tips and guidance on successful cold-weather pours, feel free to contact the BuildBlock Technical Team at (405) 840-3386.
Related Posts
Wall Parging for ICF Construction: What It Is, Why It’s Needed, and How to Do It Right
If you're working with Insulated Concrete Forms (ICFs), one question always comes up: how do you finish that exposed foam between the ground and your siding? The answer is wall parging—a critical step that not only protects your build but also enhances its curb appeal.
How to Install Electrical Wiring Into ICF Walls
https://youtu.be/9P9_AieEFEI Join BuildBlock COO Micah Garrett as he shows you a few quick and easy strategies for installing electrical wiring into ICF walls. Video Transcript: Hi, I'm Micah Garrett with BuildBlock Building Systems and today we're going to show you how to mount electrical boxes. We're going to go over…
BuildBlock ICC-500 Tornado Impact Testing
Although we couldn't persuade Intertek engineers to test our wall system with a real missile, we came close with our successful ICC-500 Tornado Impact Testing. This "Missile Impact Test" involved firing 15 lb. 2x4s from a high-pressure air cannon at over 100 mph! The goal was to assess how well…